Effect of Kevlar Fiber and Nano Sio2 on Mechanical Andthermal Properties of Hybrid Composites
P.S. Yadav1, Rajesh Purohit2*, Anil Kothari1 and R. S. Rajput1
1Department of Mechanical Engineering, Rajiv Gandhi Proudyogiki Vishwavidyalaya, Bhopal, (M.P.), India.
2Department of Mechanical Engineering, Maulana Azad National Institute of Technology Bhopal, (M.P.), India.
Corresponding Author E-mail: rpurohit73@gmail.com
DOI : http://dx.doi.org/10.13005/ojc/370303
Article Received on : 24-May-2021
Article Accepted on :
Article Published : 04 Jun 2021
The aim of the current investigation is an analysis of the mechanical and thermal properties of epoxy/ nano-silica/ Kevlar fiber hybrid composites. The ultrasonic vibration-assisted hand layup process was used for the preparation of composite with different weight percentages (1%, 2%, 3%, and 4%) of Nano SiO2 particles and 2 layers of the Kevlar fiber. For the evolution of mechanical properties tensile tests, hardness tests, impact tests, and flexural tests were done. For evaluation of morphological analysis Field Emission-Scanning Electron Microscopy, X-RD, and FT-IR tests were performed. A heat deflection temperature test was performed for the evaluation of the thermal characteristic of the hybrid composite. The results show the improvement of mechanical and thermal properties of the hybrid composite with increasing wt.% of nano SiO2 particles in the hybrid composites. As per the observation of experimental results, the Field Emission-Scanning Electron Microscopy,Fourier Transform Infrared Spectroscopy, and X-ray diffraction test also show the enhancement of surface morphology and chemical structure of hybrid composites. The heat diffraction test shows the improvement of thermal resistance and heat absorption capability.As per the observation of experimental results, the tensile strength, hardness, and impact strength increased up to 98%, 16%, and 42% respectively. The flexural test shows the improvement of flexural modulus and stresses 46% and 35% respectively. The heat deflection temperature of hybrid composite improves up to 30%.
KEYWORDS:Flexural Modulus; Hardness; Impact Strength; Nanocomposites; Tensile Strength
Download this article as:
Copy the following to cite this article: Yadav P. S, Purohit R, Kothari A, Rajput R. S. Effect of Kevlar Fiber and Nano Sio2 on Mechanical Andthermal Properties of Hybrid Composites. Orient J Chem 2021;37(3). |
Copy the following to cite this URL: Yadav P. S, Purohit R, Kothari A, Rajput R. S. Effect of Kevlar Fiber and Nano Sio2 on Mechanical Andthermal Properties of Hybrid Composites. Orient J Chem 2021;37(3). Available from: https://bit.ly/3vWgiha |
Introduction
A composites material has excellent Mechanical, Thermal and Tribological properties. Composite materials are characterized by high strength, high stiffness, or modulus of elasticity characteristics, compared to other materials. Filler and fibers enhance the performance of the composites. Epoxy and Glass fiber hybrid composites show better tribological and mechanical properties as compared to carbon-epoxy (C-E) composites in different loading conditions and speeds [1]. Nano silica particles improve the wear behavior and thermal performance of the nomex fiber composites [2]. The tensile strength and wear resistance behavior of hybrid composite enhanced by the use of Glass fiber (Bi-directional) [3]. Glass fiber enhances the hardness of composites with increasing SiO2 filler content in the composites [4]. The expansion of nano-silica filler into the epoxy composite enhanced the performance of the composite [5]. The reinforcement of banana fiber in epoxy/jute composite enhanced the thermal stability of the composite [6]. The epoxy / synthesized graphene nano-sheets /carbon nano-fibers, hybrid composite shows a better flexural bending fatigue life as compared to pure epoxy [7]. STF-Kevlar fiber composite improves the durability and energy retention conduct of the composites [8]. Natural fiber such as slag and coconut shell powder enhance the thermo-mechanical properties of the epoxy/hallo site Nanotube carbon fiber composites [9].An epoxy carbon fiber multi-scale hybrid composite shows the improvement of fracture toughness, shear strength, and fatigue crack growth rate of the hybrid composites [10]. The epoxy/glass fiber/carbon fiber mixture composite shows better flexural strength when contrasted with plain polymer composite [11]. Carbon fiber and carbon nano-tubes enhanced the toughness and strength of the epoxy-based hybrid composite. Carbon nano-tubes consistently spread in the lattice and improve the interfacial holding and strength of the composites [12]. Nano filler enhanced the absorption performance of epoxy composite [13]. Elastic and flexural properties of the composite improve with the expansion of Glass fiber [14].Nano filler enhanced the toughness and strength of the nano-composites [15]. Malefic anhydride grafted polypropylene (coupling agent) improves bonding strength and heat resistance properties of hybrid composites [16]. Kevlar fiber woven mat enhanced the toughness of epoxy-based hybrid composites [17]. Nano silica particles increase impact strength, flexural strength, and deformation of epoxy – Carbon fiber composites, and decrease absorbed energy[18]. The natural fiber composites such as rubber, sisal, jute, and glass enhanced the tensile and flexural strength of the hybrid composites. The addition of silicon carbide nanoparticles in hybrid composite also improves the wear behavior of the composites [19]. Kevlar fiber enhances the mechanical and antimicrobial properties of the composite [20]. The reinforcement of fiber in epoxy composite enhanced the density and thickness swelling properties of composite [21]. The armed carbon fiber enhanced the strength and flexural performance of the carbon armed/epoxy composites [22]. The addition of Kevlar fiber and flax fiber improves the mechanical and flexural performance of the hybrid composite [23]. One-dimensional carbon nano-fiber and graphene nano-platelets improve cyclic-fatigue loading and fracture strength of the epoxy hybrid composite [24]. Nano SiO2 filler enhanced the tribological and mechanical performance of the hybrid composite [25]. The addition of carbon nanotubes (CNTs) and a few-layer of graphene nano-platelets (GNPs) in epoxy and multi-scale composites enhanced the performance of hybrid composites [26]. Natural fiber such as mango/ shorea robust wood improved the crystalline and dynamic mechanical behavior of the hybrid composite [27]. Epoxy/ carbon fiber/ graphene oxide hybrid composite shows better electrical and mechanical properties as compared to another polymer composite [28]. Carbon fiber-enhanced toughness and strength of epoxy-based hybrid composite [29]. Water -dispersible butadiene rubber enhanced tribological and dielectric performance of the styrene-butadiene rubber nano-composites [30]. Thickness and curvature improve the impact strength of the hybrid composite [31].The graphene oxide embedded carbon fiber epoxy composite showing better flexural modulus and strength. The addition of graphene oxide increased the bonding strength of the composite [32]. The addition of graphitic nano-platelets in epoxy carbon fiber hybrid composite increased the flexural strength, shear strength, and elastic properties of hybrid composite [33]. The graphene nano-platelets increased the tensile strength and hardness of hybrid carbon fiber composites [34]. The addition of carbon armed fiber in the epoxy matrix improves the residual flexural strength of the hybrid composites [35]. The addition of glass fiber improves the wear resistance of the hybrid composites [36].Natural fiber such as slag and powder of coconut shell enhances the performance of the epoxy/hallo site Nano-tube carbon fiber composites [37]. The addition of graphene oxide in flax fiber/ epoxy composite increased the interfacial shear strength up to 43% [38].
In the current research, the effect of nano SiO2 particles (silica) in epoxy Kevlar fiber hybrid composite was assessed to find the physical, mechanical and thermal behavior. Very few studies have been done on this type of composite with different percentages of silica and Kevlar fiber. Nanocomposites with different weight percent (1, 2, 3, and 4wt.%) of nano SiO2 particles and 2 layers of Kevlar were prepared via hand layup method with ultra-sonication technique, and their physical, mechanical, thermal properties were examined. FE-SEM was used for analyzing the dispersion of nano SiO2 particles in a polymer matrix.
Composite preparation
Epoxy resin LY-556 was used as a base material and nano-silica particles (30-40nm) as filler materials. For obtaining sufficient strength in composites hardener (HY-951) was used. Kevlar fiber bidirectional woven mat was used for the preparation of hybrid composites. To make the ideal extent of epoxy/nano SiO2particles, the different weight level of SiO2 is utilized i.e. 1, 2, 3 and 4wt% for preparation of hybrid composites. An ultrasonic vibration-assisted hand layup process was used for preparing the samples of hybrid composites. To improve the bonding strength between epoxy and nano-silica particles, a coupling agent (acetone) was used. A magnetic stirrer was used for making a homogeneous mixture of nano-silica and epoxy resin.For fabrication of nanocomposites preheating of nano SiO2 particles is done for 2Hrs at 100oC in a muffle furnace. Epoxy is heated to 75oC to reduce its viscosity. Approximate 2tbsp of acetone is added which acts as a coupling agent. This mixture is put for magnetic stirring for around 90 min at 600 rpm at 85oC. After this process epoxy and nanoparticle solution is kept in an ultrasonic bath for 30min at 80oC. The mechanical stirring process was used for 30 min at 400 pm. Mixture degassed by passing nitrogen gas for 5min. After the solution comes to room temperature hardener is added in suitable proportion. The small amount of mixture is poured into the die and spread one layer of Kevlar fiber and press with the help of a roller for removing the air bubble. After that, the mixture is poured into the die and spread the second layer of fiber and the remaining mixer fill into the die and left for 24 hours for proper curing. The samples are coded with K0(Epoxy / Kevlar fiber), K1 (Epoxy / 1wt % nano SiO2 / Kevlar fiber), K2 ((Epoxy/2wt % nano SiO2 /Kevlar fiber), K3 (Epoxy/3wt % nano SiO2 /Kevlar fiber), and K4 (Epoxy/4wt % nano SiO2 /Kevlar fiber).
Experimental procedure
Physical properties test
Density test
Archimedes’s principle was employed for measuring the density of the sample material. The density of blends/composites was determined by using a liquid Piknometer / microbalance of Citizen make Model-CX265. The density of the blends/composites was determined by the method of measuring the mass and volume of the specimen used. The test specimens were cut 20x20x4 mm in size according to ASTM D570. The density was also determining theoretically using a rule of mixture.

Where Wf, Wm and are the weight % of silica particle, fabric, and matrix respectively and ρf, ρp, and ρmare the densities of fabric, particles, and matrix respectively.
The void content of the hybrid composites was calculated from the difference between the actual and theoretical densities using the following Equation.
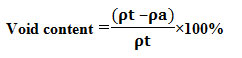
Whereρaandρtare actual and theoretical densities respectively
Water Absorption Measurement
Three specimens of 20 *20 *4 mm3 were prepared for the testing as per the ASTM D570. Before the testing the all samples are preheated in the oven at 60°C for 24 hours for removing the moisture content. After drying all samples are submersed in a distilled water-filled glass beaker for 7 days. After the test weight of submersed samples calculated and compared with the original specimen. The room temperature was set at 23°C and RH 50% for the test. All samples were checked and averaged value was taken. Water absorption % was evaluated by the following Equation.

Where,
Wo = Weight of Specimens at dry condition
Wl= Specimens weight at wet condition
Three specimens of 20* 20* 4 mm3 size were prepared for the polymer composites. ASTM D570 is used for preparing samples of composite samples. The thickness swelling was calculated by the following equation.

Where,
To = Specimens thickness at dry condition
T1= Specimens thickness at wet condition
Mechanical testing
In mechanical testing Hardness test, tensile test, impact test, and flexural test were performed.
Hardness test
The hardness of the composite at different wt% of nano-silica was evaluated with the help of a shore hardness tester in the Nano Composite Lab, MANIT- Bhopal. The samples were made according to the ASTM standard. The samples were cut in 20mm*20mm size and performed the test. For obtaining the optimum value of hardness average of three samples of each wt% was calculated and reported.
Tensile test
The samples were made as per the ASTM D638 standard and tests were done on UTM. The gauge length of the samples is 115mm, width is 13.50 mm and thickness is 5.50 mm. The tensile test was done on constant loading conditions at 100 mm/min at room temperature. The tensile test is used to calculate the young modulus, tensile strength, and elongation. For obtaining the correct value of tensile strength the three samples of each wt% were tested and the average values were reported.
Flexural test
For analyzing the flexural properties of the composites samples were tested on an Instron-3382 testing machine in Central Institute of Petrochemicals Engineering & Technology (CIPET), Bhopal. The samples were prepared as per the ASTM standard and flexural properties were calculated. For obtaining the correct value of flexural properties average of three samples of each wt.% was calculated and reported.
Impact test
Impact test was done in Central Institute of Petrochemicals Engineering &Technology (CIPET), Bhopal. The Tinius Olsen, USA make impact tester was used for calculating the impact strength of the composites. The samples were prepared as per the ASTM standard and a notch was made with the help of notch making machine and calculate the impact strength of the composites. For obtaining the optimum value of impact strength the average of three samples of each wt% were calculated and reported.
Characterization of polymer composite
FE-ESM set up JSM 5600 (make JEOL/EO, Japan) was used for the analysis of surface texture and distribution of nanoparticles in the polymer composites. Fourier Transform-Infrared (FT-IR) spectrometer (BRUKER – ALPHA) was used to characterize the chemical structure of polymer matrix composites. FT-IR was carried out at transmittance mode within the range of 3500 to 1000 cm-1. An X-ray diffraction test was done for structural analysis of composite samples at MSME laboratory, Maulana Azad National Institute of Technology, Bhopal.
Thermal Characterization of hybrid composites
Thermal properties of the hybrid composite such as thermal stability, heat absorption capacity of the composite were evaluated byheat deflection temperature test.Heat diffraction test done on GLOBE, Hear deflection temperature tester in Nanocomposite laboratory, MANIT Bhopal. The samples were cut in (120mmx8mmx6mm) size as per the ASTM D648 standard. The heat deflection temperature of the composite wasmeasured in standard pressure of 100psi (0.68MPa) and 0.30mmdeflection.
Results and discussions
Physical properties test
Density test
Table 1: Density and void content of hybrid composites
Composite Samples |
Theoretical Density (gm/cm3) |
Experimental Density (gm/cm3) |
Void content in % |
K0 |
1.208 |
1.197 |
0.91 |
K1 |
1.214 |
1.191 |
1.89 |
K2 |
1.222 |
1.174 |
3.27 |
K3 |
1.226 |
1.163 |
4.07 |
K4 |
1.232 |
1.153 |
5.66 |
The theoretical density of hybrid composite was measured by the ROM and actual density was measured by picknometer. As per the observation, the density of the composite increased with increasing the wt.% of nano-silica and Kevlar fiber in the composites. Minimum density is observed at 1wt% and maximum density is observed at 4wt%. The void content was also increased with increasing the wt% of nano SiO2 in the hybrid composites [21]. The maximum void content was observed in 4wt% nano SiO2 particles.
Water absorption and thickness swelling test
Water absorption test results are shown in figure 1. The composite sample’s water absorption capacity is very low due to the hydrophobic nature of the epoxy [13]. When nano SiO2 particles were reinforced in the composite the water absorption behavior was increased. Kevlar fiber reduced the absorption behavior of the hybrid composites. Neat epoxy showing low water absorption and after that, it was increased. Maximum absorption was shown by the K4 sample. Thickness swelling test results are shown in figure 2. The composite sample’s thickness swelling capacity is very low due to the hydrophobic nature of the epoxy [21]. When nano SiO2 particles and Kevlar fiber were reinforced in the composite the thickness swelling behavior was increased. Neat epoxy showing low thickness swelling and after that, it was increased. Maximum absorption was shown by the K4 sample.
![]() |
Figure 1: Water absorption v/s Nano silica particles. |
![]() |
Figure 2: Thickness swelling v/s nano-silica particles. |
Mechanical properties test
Hardness test
Figure 3 shows that the hardness of the hybrid composite improved with nano-silica particles and Kevlar fiber. The above results show the value of hardness increase with increasing the wt% of nano-silica in the hybrid composites. The maximum value of hardness was found with 4 wt% of composites. The hardness of the composite improves the surface morphology and strength of the hybrid composites [2]. The maximum value of hardness was obtained with 4% of nano SiO2 particles. The addition of nano SiO2 particles and Kevlar fiber in epoxy resin improves the hardness of hybrid composite up to 16%.
![]() |
Figure 3: Hardness v/s nano-silica in hybrid composites. |
Tensile test
The tensile test results showed if figure 4 and 5 depicts the improvement of tensile strength with growing wt.% of the nano SiO2 particles in the hybrid composites. The maximum value of tensile strength was found with 3 wt.% and after that, it is gradually decreased. The maximum value of elongation was obtained with 1 wt.% and after that, it was decreased. This trend shows the brittleness of composites increases with higher loading of nano-SiO2 particles. Kevlar fiber and nano SiO2 particles in the hybrid composite increased tensile strength up to 98% and decreased the elongation properties up to 60%. Reduction in tensile strength is caused by non-uniform desperation and agglomeration of nanoparticles with the matrix material [3].
![]() |
Figure 4: Tensile Stress v/s nano silica particles. |
![]() |
Figure 5: Elongation v/s nano silica particles |
Flexural test
Figures 6 and 7 show that the flexural properties of composite enhanced with high wt% of the SiO2 nanoparticles and Kevlar fiber up to 3wt% in hybrid composites. Nanoparticles were easily mixed with epoxy and enhanced the strength of hybrid composites [14]. The mixing of nanofiller increases flexural stress and modulus up to 3wt% and after that, it is decreasing gradually because of limitations of nano SiO2 particles at higher wt%. As per the results, the addition of Kevlar fiber and nano-filler increase flexural stress and modulus up to 35%, and 46% respectively.
![]() |
Figure 6: Flexural stress v/s nano-silica particles. |
![]() |
Figure 7: Flexural Modulus v/s nano-silica particles. |
Impact test
Increasing the wt% of nano SiO2 in the hybrid composite enhances the impact strength up to 3wt%.Nanoparticles equally dispersed in resin and improve the hardness and reduced the toughness of composites. The maximum value of impact strength observer with 3 wt% of SiO2 nanoparticles and the minimum value is obtained with 1wt%. The addition of Kevlar fiber and nanofiller increase impact strength up to 42%. Uniform desperation of nanoparticles and interlock mechanism between nanoparticles and epoxy are the two important factors for improving the impact strength of the composites [10].
![]() |
Figure 8: Variation of Impact strength with wt% of nano-silica particles. |
Characterization of hybrid composites
FE-SEM test
FE-SEM results show the improvement of surface morphology of the hybrid composites. As per the image’s nano, SiO2 particles were properly mixed with the epoxy and uniformly dispersed in the composite. At lower loading of nano SiO2 particles in the epoxy shows small clustering [22]. The high loading of nano-silica particles increased the tendency of agglomerations. The size of the agglomerations increased with higher wt% of the nano SiO2 particles in the composites. The maximum agglomerations formed in the K4 sample. Lump formation in the composite also increased with high wt% of nano-silica particles and it decreases mechanical properties of hybrid composites.
![]() |
Figure 9: FE-SEM images of Kevlar fiber hybrid composite. |
FT-IR test
The FT-IR results show the improvement of the vibration frequency of hydrogen and carbon with oxygen. The carboxyl group (-C=0) frequency improved from 1694 to 1696 cm-1and hydroxyl group (-OH) 3742 to 3743 cm-1. The reinforcing of nano-silica filler in the epoxy increased the vibration frequency of Si-OH from 3836 to 3893 cm-1. The uniform dispersion of nanoparticles enhanced the bonding strength between the epoxy and nanofiller. Due to high strength, the mechanical performance of the epoxy composite was improved. The nanoparticles uniformly speared in the surface of the Kevlar fiber and create a strong bonding between nanofiller and fibers [38]. It is the main cause of improving the surface morphology, mechanical properties, and heat deflection temperature of the hybrid composites.
![]() |
Figure 10: FT-IR graphs for Hybrid Composites. |
X-Ray Diffraction test
The XRD results (Figure 11) show the variation of intensity with K1, K2, K3, and K4 samples. The maximum intensity of composite was found with 4wt% of nanoparticles. The intensity is maximum between 20 to 25° which shows the proper mixing of filler nano SiO2and epoxy. As per result the intensity of hybrid composite are 2300-2800au. This is showing the semi-crystalline behavior of the hybrid composites.
![]() |
Figure 11: Variation of the intensity of a hybrid composite. |
Heat deflection temperature test
Heat deflection temperature test results show the improvement of the heat resistance capacity of hybrid composites. Pure epoxy is a soft material and showing lower heat resistance properties. The addition of nano SiO2 particles and Kevlar fiber in the epoxy improves the heat resistance performance of the composites. The nanoparticles are uniformly distributed in the composite and enhanced heat absorption capacity and reduced the deflection tendency of the composites [6]. The Kevlar fiber also improves the heat absorption capacity of the hybrid composites. The addition of fiber in the matrix increased the deflection temperature of hybrid composite, due to good heat resistance properties. The sample K4 shows the maximum heat deflection temperature [6].
![]() |
Figure 12: Variation of deflection temperature of hybrid composite. |
Conclusions
As per the above experiments following results are obtained:
Physical properties like density and void content test results show the density and void content of hybrid composite increasing with nano SiO2 particles in the composites. Thickness swelling and water absorption test showing the incensement with increasing wt% of nano SiO2 particles. Mechanical properties of the hybrid composite improve with the use of nanofiller and Kevlar fiber. The hardness test shows the16% improvement in hardness of composites. The tensile test shows the improvement of tensile strength up to 3wt%. The nano-silica particles enhance the tensile strength up to 98% and decreased the elongation properties up to 60%. Impact test shows the improvement of impact strength up to 42%. Flexural tests show the improvement of flexural modulus and flexural strength up to 46% and 30% respectively by the addition of nano SiO2 particles.
Characterization of hybrid composite shows the improvement with the loading of nanofiller and Kevlar fiber in the polymer matrix. FE-SEM results show the proper distribution of nano-particles in the hybrid composites. FT-IR results show the enhancement of intermolecular bond strength between the epoxy and nano-silica particles and enhance the mechanical properties of composites. XRD results show the enhancement of surface morphology and crystalline structure of composites. Heat deflection temperature test shows the improvement in thermal performance of the hybrid composite with increasing wt% of nano-silica particles. The heat deflection temperature improved up to 30%.
References
- Suresha B., Chandramohan G., Samapthkumaran P., Seetharamu S., Vynatheya S.,J.O. Reinforced Plastics and Comp., 2006, 25, 771-782.
CrossRef - Su Feng-Hua, Zhang Zhao-Zhu , Liu Wei-Min, Comp. Sci.& Tech., 2007, 67, 102–110
- Harsha A.P., Jha Sanjeev Kumar, Wear, 2008, 265, 1129–1135.
CrossRef - Yueping Ye, Haibin Chen, Jingshen Wu, Chi Ming Chan, Comp. Part B, Engineering, 2011, 42, 2145-2150.
CrossRef - Raju B.R., Swamy R.P., Bharath B. K. N., Advances in Polymer Scie.& Tech. 2012,02, 51-57.
CrossRef - Boopalan M., Niranjanaa M., Umapathy M.J., Comp. Part B, 2013, 51, 54-57.
CrossRef - Shokrieh M.M., Esmkhani M., Haghighatkhah A.R., Zhao Z., Materials and Design, 2014, 62, 401-408.
CrossRef - Majumdar Abhijit, Butola Bhupendra Singh, Srivastava Ankita, Materials and Design, 2014, 54, 295-300.
CrossRef - Rostamiyan Y, Hamed Mashhadzadeh A, Salman Khani A., Material and Design, 2014, 56, 1068-1077.
CrossRef - Fenner Joel S., Daniel Isaac M., Comp. Part A, 2014, 65, 47-56.
CrossRef - Dong Chensong, Kalantari Mehdi, Davies Ian J., Comp. Structures, 2015,128, 354-362.
CrossRef - Sharma S.P., Lakkad S.C., Comp. Part A, 2015, 69, 124-131.
CrossRef - Mallam Yakubu Dan, Hong Tan Wei, Majid Shukry Abdul, I. J. of Poly. Science, 2015, 01, 1-13.
CrossRef - Madhsudhan T, M Senthil kumar, Athith D, I. R. J of Engg. & Tech. (IRJET), 2016,03(04), 2243-2246.
- E Edison, Odeshi Haro Akindele G, Szpunar Jerzy A, I. J. of Impact engg., 2016, 96, 11-22.
CrossRef - Bandaru Aswani Kumar, Chavan Vikrant V, Ahmad Suhail, Alagirusamy R, Bhatnagar Naresh, I. J. of Impact Engineering, 2016, 89, 1- 13.
CrossRef - Bresciani L.M, A. Manes A, A. Ruggiero A, G. Iannitti G, M. Giglio M., Comp. Part B,2016, 88, 114-130.
CrossRef - Landowski M, Strugała G, Budzik M, Imielińska K, Comp. Part B., 2017, 113, 91–99.
CrossRef - Madhusudhan T., Senthil Kumar M., I. J. of Mechanical Engg. & Tech. (IJMET), 2017, 08(02), 82–92.
- Balagna Cristina, Irfan Muhammad, Perero Sergio, Miola Marta, Giovanni Maina, Santella Daniela, Simone Antonia, Surf. A. Coat. Tech., 2017, 321, 438–447.
CrossRef - Atiqah A., Jawaid M., Ishak M. R., Sapuan S. M., Procedia Engineering,2017, 184, 581-586.
CrossRef - B Ruban Rajasekar, Asokan R, Senbagan M, Karthika R, Sivajyothia Kethavarapu, Sharma Nishtha, Materials Today: Proce., 2018, 05, 25323-25330.
CrossRef - Audiberta Clement, Andreania Anne-Sophie, Laineb Eric, Grandidier Jean-Claude, Comp. Structures, 2018,195, 126-135.
CrossRef - Ladania Raj B., Bhasina Mukesh, Wub Shuying, Ravindrana Anil R., Ghorbania Kamran, Zhang Jin, Kinlochd Anthony J., Mouritza Adrian P., Wang Chun H., Engineering Fracture Mechanics, 2018, 203, 102-114.
CrossRef - Alsaadi Mohamad, Bulut Mehmet, Erkliğ Ahmet, Jabbar Arkan, Comp. Part B., 2018, 30810-2.
- Zhou Guodong, Yao Huichao, Zhou Yang, Wang Weitao, Peng Mao, Carbon, 2018, 137, 6-18.
CrossRef - Saxena Mohit, Gupta M. K., Materials Today: Proce., 2018, 05, 19359-19366.
CrossRef - Yuana Xiaomin, Zhua Bo, Caic Xun, Qiaob Kun, Zhaoa Shengyao, Yua Junwei, Applied Surface Science, 2018, 458, 996-1005.
CrossRef - Suresha B., Adappa Karthik, Subramani Nithin Kundachira, Materials Today: Proceedings. 2018, 05, 16658-1668.
CrossRef - Chena Yang, Yina Qing, Zhanga Xumin, Zhanga Wanqi, Jiaa Hongbing, Jib Qingmin, Yang Fufeng, Rui Xiaoting, Comp. Part B., 2019, 166, 196–203.
- Andrew J. J, Kumar Siva, Srinivasan M., Arockiarajan A. Dhakal Homnath, Comp. struc., 2019, 224, 111007.
CrossRef - Hung Pui-yan, Lau Kin-tak, Fox Bronwyn, Hameed Nishar Jia , Baohua, Joong Hee Lee, Carbon, 2019, 152, 556-564.
CrossRef - Khan Nazrul Islam, Halder Sudipta, Das Subhankar, Wang Jialai, Comp. Part B, 2019, 173, 106855.
CrossRef - Pawlik Marzena, Le Huirong, Lu Yiling, Comp. Part B, 2019, 177, 107097.
CrossRef - Wagiha A, Sebaey T.A., Yudhanto A., Lubineau G., Comp. Struct, 2020, 239, 112022.
CrossRef - Arnimesh B., NayakShubham, Kumar Rajesh, Ray Bankim Chandra, Materials Today Proce., 2020, 33, 5098-5102.
CrossRef - SinhaRoopesh Kumar, Sridhar K., Purohit, Rajesh, Materials Today Proceedings. 2020, 26(02), 3183-3186.
CrossRef - Javanshour F., Ramakrishnan K. R., Layek R.K., Laurikainen P., Prapavesis A., M. Kanerva M., Kallio, A.W., Vuure Van, Sarlin E., Comp. Part A, 2021, 142, 106270.
CrossRef
This work is licensed under a Creative Commons Attribution 4.0 International License.
0 Comments